Jeder kennt sie noch, die Oldtimer aus der 2. Hälfte des 19. Jahrhunderts, als rundum offene Automobile ohne Scheiben die Regel waren. Die meist männlichen, seltener weiblichen Fahrer trugen Lederhauben und Brillen zum Schutz gegen Fahrtwind und Staub. Erst im Jahre 1904 wurde die Windschutzscheibe erfunden. Sie übernahm eine wichtige Funktion zum Schutz der Passagiere vor frontal auftretenden äußeren Einflüssen. Ab Mitte der ersten Hälfte des 20. Jahrhunderts begann dann der Siegeszug des Verbund-Sicherheitsglases. Ein als Verbund-Sicherheitsglas bezeichnetes Material besteht aus drei Schichten, einer inneren Schicht aus Polyvinylbutyral und zwei Deckschichten aus gehärtetem Klarglas. Der große Vorteil von Verbund-Sicherheitsglas ist, dass es sich leicht bei Belastung verformt und insgesamt einen sicheren Schutz gegen Splitter bietet und somit dem gesetzlich vorgeschriebenen Standard entspricht.
Dies alles und noch viel mehr erfuhren 28 Teilnehmer der Kameradschaft AACHEN/ESCHWEILER in einem Einführungsvortrag bei Saint-Gobain Sekurit GmbH in HERZOGENRATH, nachdem sie durch die Assistentin der Geschäftsführung in Empfang genommen, mit den entsprechenden Zugangsberechtigungen (Besucherausweis, Sicherheitsausrüstung) ausgestattet und zur theoretischen Einweisung durch den Produktionsleiter in den Vortragsraum geführt wurden.
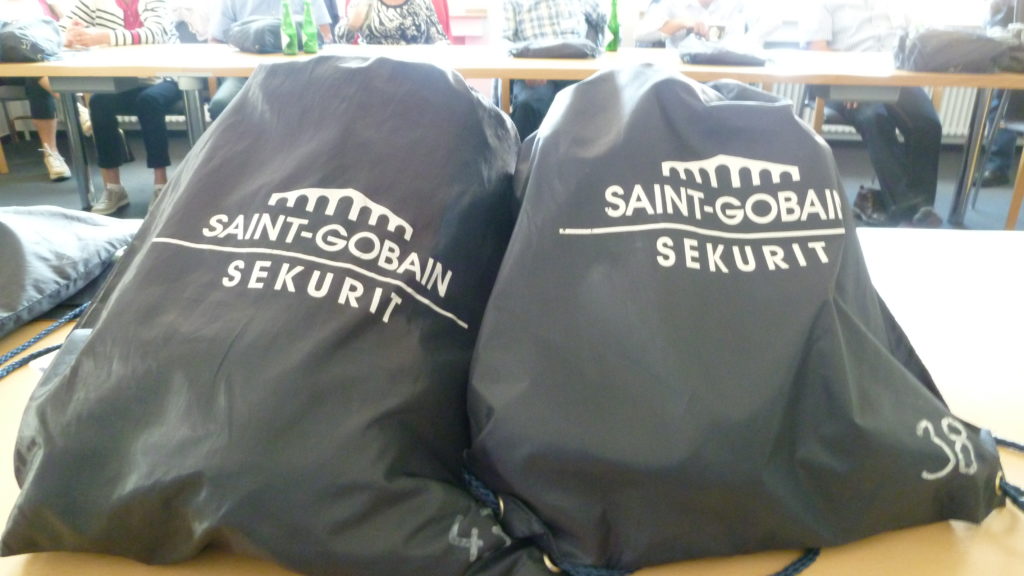
In Deutschland ist Sekurit an vier Standorten vertreten. Jedoch der größte Produktionsstandort und zugleich Firmensitz ist in HERZOGENRATH bei AACHEN. Hier arbeiten ca. 450 Mitarbeiter in den Bereichen Verwaltung, Fertigung, in der eigenen Ausbildungseinrichtung, genannt Saint-Gobain Academy 4.0, sowie im F&E-Zentrum Saint-Gobain Research Germany. Jährlich verlassen ca. 12.000.000 Autoscheiben unterschiedlicher Größen und Funktionalitäten für fast alle europäischen Automobilmarken das Werk in HERZOGENRATH.
Saint-Gobain Sekurit versteht sich als der Technologievorreiter, Innovator und Produktionsentwickler eines weltweiten führenden Konzernes im Bereich der Fahrzeugverglasung.
Bereits in den 1920-er Jahren präsentierte Saint-Gobain das Sicherheitsglas Securit. 1929/1930 wurde das Einscheiben-Sicherheitsglas, das bis in die heutige Zeit als Standard-Sicherheitsglas im Automobilbau verwendet wird, von Saint-Gobain auf den Markt gebracht.
Heute gehören zu deren Portfolio Entwicklungen von Windschutzscheiben über Türscharniere bis hin zur Dämmung von Fahrzeugkabinen. Saint-Gobain Sekurit entwickelt weiterhin eine Vielzahl innovativer Lösungen für führende Automobilhersteller. Das sind unter anderem Lösungen zur Verringerung des Kraftstoffverbrauchs, für Sensoren für Scheibenwischer und Licht, integrierte LED und Antennen, Spiegelung von Armaturen, Navigationsdaten sowie weitere für Sicherheitsaspekte, akustischen und thermischen Komfort sowie Konnektivität.
Wie werden Autoscheiben hergestellt?
Da Autoscheiben verschiedene wichtige Eigenschaften besitzen, so müssen sie
- über einen langen Zeitraum hinweg klar und durchsichtig bleiben,
- aus widerstandsfähigen Materialien hergestellt sein,
- Autodächer bei Unfällen mit Überschlägen als tragendes Element unterstützen können,
- stark genug sein, um kleineren Kollisionen zu widerstehen und, besonders wichtig,
- durch Splittersicherheit verhindern, dass bei größeren Unfällen Glassplitter durch die Luft fliegen,
wurde zuerst in der Theorie die Glasbiegeverfahren erklärt.
Der überwiegende Teil der Scheiben, die in Fahrzeuge eingebaut werden, ist gebogen. Als zwei wesentliche Biegeverfahren kommen entweder das Schwerkraftbiegeverfahren oder das Pressbiegeverfahren mit ihren Abweichungen in Frage.
Beim Schwerkraftbiegeverfahren im “Horizontalverfahren“ werden beide Scheiben eines Verbundglases, das sogenannte Glaspaar, auf das Biegewerkzeug, die Biegeform, gelegt und werden anschließend in einem Biegeofen erwärmt. Durch die Viskositätsänderung des Glases, die Schwerkraft und die Kinematik des Biegewerkzeuges, schmiegt sich die Scheibe in die Biegeform und erhält somit die gewünschte Form und Geometrie.
Das Pressbiegen erfolgt ebenfalls im Horizontalverfahren. Nachdem die Scheibe auf Rollgängen durch einen Ofenkanal transportiert und auf Biegetemperatur erwärmt wurde, erhält sie ihre endgültige Form durch einen Pressvorgang mittels eines zweiteiligen Stempels, der aus Patrize (Positiv) und Matrize (Negativ) besteht. Das Pressbiegeverfahren stellt den neuesten Stand der Glasbiegetechnik dar, gewährleistet geringste Biegetoleranzen und ermöglicht so, die gewünschte Form der Scheibe exakt bis zur Glaskante auszuformen.
Beim Glasbiegen im “Vertikalverfahren“ werden die Scheiben an mehreren Zangen an einer Kante aufgehängt und durchfahren so einen Ofen. Nach dem Austritt aus dem Ofen werden die Scheiben, ähnlich wie beim Pressbiegeverfahren, in ihre Form gebracht. Dieses Verfahren wird meisten bei Seitenscheiben aus Einscheibensicherheitsglas (ESG) angewendet, weil nach dem Biegen die Scheibe durch eine beidseitig wirkende Luftdusche vorgespannt wird.
Nach diesem auch für Nichttechniker sehr verständlichen Vortrag ging es endlich zur Produktionshalle, einer riesigen, mehrere Fußballfelder großen Halle mit 4 Produktionslinien für die Herstellung unterschiedlicher Scheiben.
Der Produktionsprozess
Der Herstellungsprozess beginnt mit der Anlieferung des Rohglases aus dem danebenliegenden, jedoch eigenständigen Werk „Saint-Gobain Floate Glass“.
Dieses vorgetemperte Glas in den Größen 6mx4m wird anschließend mit Hilfe von Diamantschneidwerkzeugen, quasi einem Glasschneider, in die benötigten Größen (Front-, Heck-, Seitenscheiben sowie Glasdächer) geschnitten. Die Glasplatte wird dann auf oder in eine Gussform gelegt, die die gewünschte Form und Biegung der Scheibe aufweist. Dort wird das Glas genau so weit aufgeheizt, dass es weich wird ohne zu schmelzen und so auf oder in die Gussform absinkt. Anschließend wird es durch kalte Luftströme extrem schnell abgekühlt. Dieses Tempern stärkt und härtet das Glas in hohem Maße.
Im letzten Schritt zur Herstellung von Verbundglasscheiben wird eine Lage getemperten Glases auf jede Seite einer sehr dünnen Schicht aus Polyvinylbutyral (PVB) aufgebracht. Der Verbund wird in einem Autoklaven erhitzt und zwischen Rollen gepresst. Dieser Schritt macht das PVB transparent und verschmilzt die Glaslagen und das PVB zu einer einzigen Verbund-Sicherheitsglasscheibe.
In das nun schon einer richtigen Autoscheibe ähnelnte Glas können nun verschiedene Sensoren, Zusatzfunktionen und Auflagen der Autohersteller eingearbeitet werden. Diese reichen von Regensensoren bis zu Vielzweckantennen oder wasserabweisenden Beschichtungen. Zusätzlich versieht Saint-Gobain jede Scheibe mit ihren individuellen Herstellungsparametern. Damit können Fehler oder Reklamationen jederzeit punktuell nachvollzogen werden.
Nach den Zwischen- und Endkontrollen wäre jetzt die Windschutzscheibe fertig zum Einbau und könnte mit Hilfe von speziellen polyurethan- oder „urethan-“haltigen Primern, Kleb- und Dichtstoffen in die Karosserie des Fahrzeugs eingeklebt werden. Dies geschieht dann nach dem Versenden in den Werken der jeweiligen Autohersteller.
Das Bemerkenswerteste unseres Besuches war jedoch die Produktionslinie im Industriestandard 4.0. Hier lief der Herstellungsprozess der Autogläser überwiegend autonom ab, nur gesteuert aus einem Container anhand von riesigen Wandmonitoren, die interaktiv alle Parameter, wie Energieverbrauch, hergestellte Stückzahlen, Funktionsfähigkeit einzelner Arbeitsschritte und Maschinen ebenengerecht abbilden. Dies setzt natürlich eine Vernetzung alleine von über 4.500 verbauten Sensoren voraus. So war es eigentlich nur logisch, dass in der riesigen Produktionshalle kaum Mitarbeiter zu sehen waren. Die Masse der Arbeiten erledigten Automaten, Roboter und Förderbänder. Wenn nötig, lieferten autonom fahrende Transportmaschinen auf festgelegten Strecken halbfertige Produkte von einem Band zum anderen. So muss man sich eben die Fabriken der Zukunft vorstellen
Am Ende der Führung übereichte unser Vorsitzender, Oberst a.D. Günter Selbert, unser Vereinswappen an die Assistentin der Geschäftsführung und bedankte sich für diese gut durchdachte und sehr beeindruckende Führung durch den Produktionsprozess von Autoscheiben.
Im Anschluss war es selbstverständlich, das eben Erlebte in gemütlicher Runde in der nahegelegenen Kloster Brasserie der altehrwürdigen Abtei Rolduc in KERKRADE, eines der wichtigsten religiösen Denkmäler der Niederlande und des größten Abteikomplexes der Benelux-Länder insgesamt, bei Kaffee mit Kuchen ausklingen zu lassen.
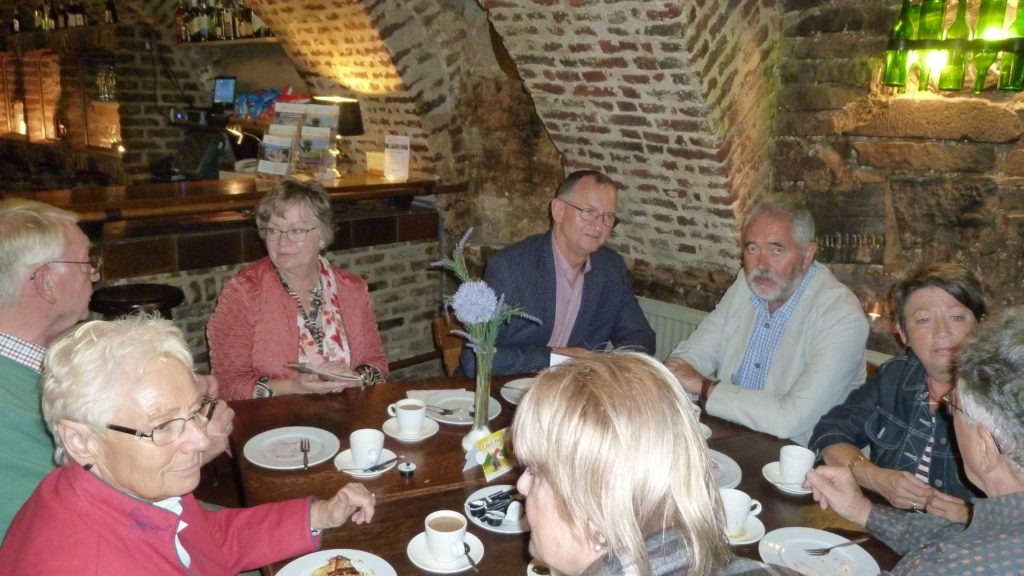
Autor und Fotos: Oberstleutnant a.D. J. Steibel